Curing of concrete techniques
Curing techniques
Curing is the protection of fresh concrete from evaporation and temperature extremes which might adversely affect cement hydration. If concrete is to gain potential strength and durability it must have sufficient water for the hydration of the cement, and a temperature conducive to maintain this chemical reaction at a rapid, continuous rate.
To ensure the existence of these conditions, the concrete must be protected from the harmful influences of wind, sun and variable weather. As 23°C is considered the ideal temperature for hydration, it is desirable to maintain concrete temperature at or about this figure as curing proceeds.
Concrete curing techniques fall into two groups - those designed to prevent loss of water, such as the application of impermeable membranes; and those that supply moisture throughout the early stages of the hydration process, such as ponding or the application of wet sand or hessian.
Selecting the method of curing is generally a matter of economics, but another consideration is that the method used should cause the least interference to other operations on the site.
Evaporation from concrete freshly placed on site
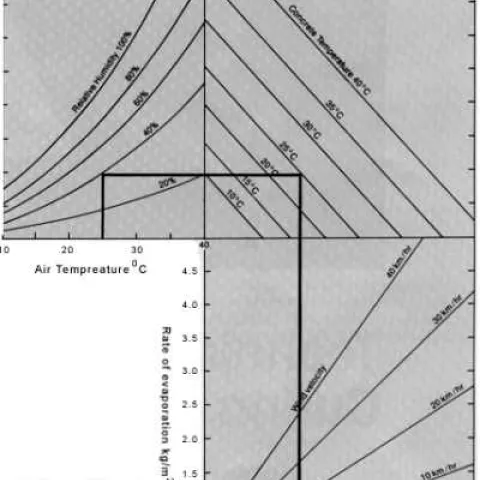
The graph shows the effects of air temperature, humidity, concrete temperature, and wind velocity together on the rate of evaporation of water from freshly placed and unprotected concrete.
Example:
- With air temperature at 25°C
- With relative humidity at 40%
With concrete temperature at 25°C - With a wind velocity of 20 km/hr the rate of evaporation would be 1.1 kg/m² hr. The highlighted line plots the example described above. The nomogram can be used for calculation of evaporation rates if other variables are known.
To determine the evaporation rate from the graph enter the graph at the air temperature (in this case 25°C and move vertically to intersect the curve for relative humidity encountered - here 40%. From this point move horizontally to the respective line for concrete temperature - here 25°C. Move vertically down to the respective wind velocity curve and then horizontally to the left to intersect the scale for rate of evaporation.
Trouble with plastic cracking is potentially in the making when the rate of evaporation exceeds 0.5 kg/m² hr.
When the evaporation rate exceeds 1.0 kg/ m² hr precautionary measures to prevent plastic shrinkage are almost mandatory.
Water retaining materials
Chemical or liquid membranes are gaining in popularity because they are convenient to use. They can be applied by hand or power sprays.
These membranes come in four general categories: water based; chlorinated-rubber based; resin based and PVA based.
In addition to the above classification, curing compounds can be purchased in three different types: Type 1 is clear and translucent without dye; Type1-D clear and translucent with fugitive dye; Type 2, white pigmented.
The clear types usually preferred for surfaces that must be architecturally attractive have one major disadvantage; it is difficult to determine whether they have covered an area of concrete completely.
White compounds reflect the rays of the sun, greatly reducing the surface temperature of the concrete. The white colour will make the covered areas easily distinguishable. After a few days of exposure to direct sunlight the colour will fade.
When it dries, a membrane compound forms a vapour seal on the surface, and the hardness of the sealer film when dry, are important factors.
Care should be exercised in the selection of an appropriate membrane coating in that compatibility with the intended applied finish to the concrete must be taken into account.
Mechanical barriers
The use of waterproof building papers or plastic film (polyethylene sheeting) will also prevent the evaporation of moisture from concrete.
Pigmented polyethylene sheeting provides a good curing medium as it is impervious to moisture, light in weight, and can be re-used under good conditions.
Plastic sheeting also has the advantage of flexibility. It is easy to drape over complex shapes, and the progress of curing and condition of the concrete can be checked easily at any time.
Any material used as a mechanical barrier to evaporation should be placed over the concrete as soon as the placing of it will not cause surface damage. The edges of the material should overlap several inches, and should be tightly sealed with sand, tape, mastic or wooden planks.
It is a good practice - though one not always followed - to moisten the surface of the concrete with an atomising spray of water immediately prior to placing of the sheeting on the concrete.
Water addition curing
Theoretically, flooding, ponding or mist spraying are better than the retention methods mentioned above. But they are not always practical because of job conditions.
On roads, pavements or floors, the method of flooding or ponding is simple. A small dam of earth or other water retaining material is placed around the perimeter of the surface and the enclosed area is kept flooded with water.
Continuous spraying with water, while somewhat easier to control than ponding, is subject to such difficulties as nozzle clogging and loss of water pressure. In the spraying method the water is forced through horizontal pipes to various locations and out through nozzles which disperse it over the concrete surface.
Fogging is essentially the same, but the nozzles deliver a finer, mist like spray. Both methods are affected by changes in wind velocity, which can considerably reduce their effectiveness.
Care should be exercised to prevent large temperature differentials between the concrete mass and curing environment so as to avoid potential cracking due to temperature gradients within the concrete. This is generally known as thermal shock cracking.
Absorptive covers
An absorptive medium such as sand, hessian or canvas will hold water on the concrete surface while curing progresses.
Any such medium must be kept damp constantly during the curing period, for if drying is permitted, the cover itself will absorb moisture from the concrete. Alternate drying out and wetting of the cover may cause cracking.
The use of sawdust as a cover is not advisable, for it has on occasion retarded the hardening of the concrete through the action of sugar in the sap still present in the sawdust.
Structural concrete
The curing of structural concrete does not present as many problems as may be experienced in curing thick floor slabs or pavements, because the exposed surfaces are usually smaller.
Many concrete structures receive no curing other than that effected by leaving forms in place for several days. The insulating value of formwork is self-evident, but as a curing medium formwork is effective only for the first day or so. As drying proceeds, water vapour can escape along the gaps between the forms and concrete, as well as through gaps between boards.
If formwork is to have a complete curing function it must be kept wet continuously.
Exposed surfaces of the structure should be covered with tarpaulins, plastic sheeting or waterproof paper, and kept wet.
When a concrete structure is built without protection of any kind, the concrete being allowed to harden while exposed by turns of sunlight, evening temperatures, wind and rain, inferior strength and durability of concrete frequently results.
Reasons for curing
To sum up the advantages of careful control of moisture and temperature in curing:
- The strength of concrete increases with age if curing conditions are favourable. Compressive strength of properly cured concrete is 80 to 100 per cent greater than the strength of concrete which has not been cured at all.
- Properly cured concrete surfaces wear well.
- Drying, shrinkage, cracking is reduced.
- Greater watertightness of constructions is assured.
Points to keep in mind when curing:
- Start curing operations as soon as possible after concrete has been placed.
- For proper curing concrete needs moisture.
- Continuity in curing is a must; alterations of wetting and drying promote the development of cracking.
- If during curing the concrete is allowed to dry out - as may happen in hot weather - the chemical stops right at the point where the concrete loses its moisture.
- The ideal curing temperature is 23°C.
- Cure concrete for at least 7 days.
The vicious cycle in inadequate curing must be obvious. If enough water evaporates from the concrete before it has attained its maximum strength, there will not be sufficient water remaining in the concrete to fully hydrate the cement and so achieve that maximum strength.